Check our M-Series (Metallic) and D-Series (Ceramic) catalytic converters designed especially for diesel engines…
What Is a Diesel Oxidation Catalyst?
Diesel Oxidation Catalysts (DOC) are catalytic converters designed specifically for diesel engines and equipment to reduce Carbon Monoxide (CO), Hydrocarbons (HC) and Particulate Matter (PM) emissions. DOC's are simple, inexpensive, maintenance-free and suitable for all types and applications of diesel engines.
Figure 1. How Diesel Oxidation Catalyst (DOC) Works
Modern catalytic converters consist of a monolith honeycomb substrate coated with platinum group metal catalyst, packaged in a stainless steel container. The honeycomb structure with many small parallel channels presents a high catalytic contact area to exhaust gasses. As the hot gases contact the catalyst, several exhaust pollutants are converted into harmless substances: carbon dioxide and water.
The diesel oxidation catalyst is designed to oxidize carbon monoxide, gas phase hydrocarbons, and the SOF fraction of diesel particulate matter to CO2 and H2O:
Diesel exhaust contains sufficient amounts of oxygen, necessary for the above reactions. The concentration of O2 in the exhaust gases from diesel engine varies between 3 and 17%, depending on the engine load. Typical conversion efficiencies for CO and HC in the Nett® diesel oxidation catalyst are given in Figure 2. The catalyst activity increases with temperature. A minimum exhaust temperature of about 200°C is necessary for the catalyst to "light off". At elevated temperatures, conversions depend on the catalyst size and design and can be higher than 90%.
Figure 2. Catalytic Conversion of Carbon Monoxide and Hydrocarbons
Conversion of diesel particulate matter is an important function of the modern diesel oxidation catalyst. The catalyst exhibits a very high activity in the oxidation of the organic fraction (SOF) of diesel particulates. Conversion of SOF may reach and exceed 80%. At lower temperatures, say 300°C, the total DPM conversion is usually between 30 and 50% (Figure 3). At high temperatures, above 400°C, a counterproductive process may occur in the catalyst. It is the oxidation of sulfur dioxide to sulfur trioxide, which combines with water forming sulfuric acid:
A formation of the sulfate (SO4) particulates occurs, outweighing the benefit of the SOF reduction. Figure 3 shows an example situation, where at 450°C the engine-out and the catalyst total DPM emissions are equal. In reality the generation of sulfates strongly depends on the sulfur content of the fuel as well as on the catalyst formulation. It is possible to decrease DPM emissions with a catalyst even at high temperatures, provided suitable catalyst formulation and good quality fuels of low sulfur contents are used. On the other hand, diesel oxidation catalyst used with high sulfur fuel will increase the total DPM output at higher temperatures. This is why diesel catalysts become more widespread only after the commercial introduction of low sulfur diesel fuel.
Figure 3. Catalytic Conversion of DPM
The diesel oxidation catalyst, depending on its formulation, may also exhibit some limited activity towards the reduction of nitrogen oxides in diesel exhaust. NOx conversions of 10-20% are usually observed. The NOx conversion exhibits a maximum at medium temperatures of about 300°C.
Nett Technologies’ Diesel Oxidation Catalysts (DOC)
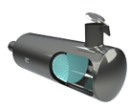
Request A Quote
Photo Gallery